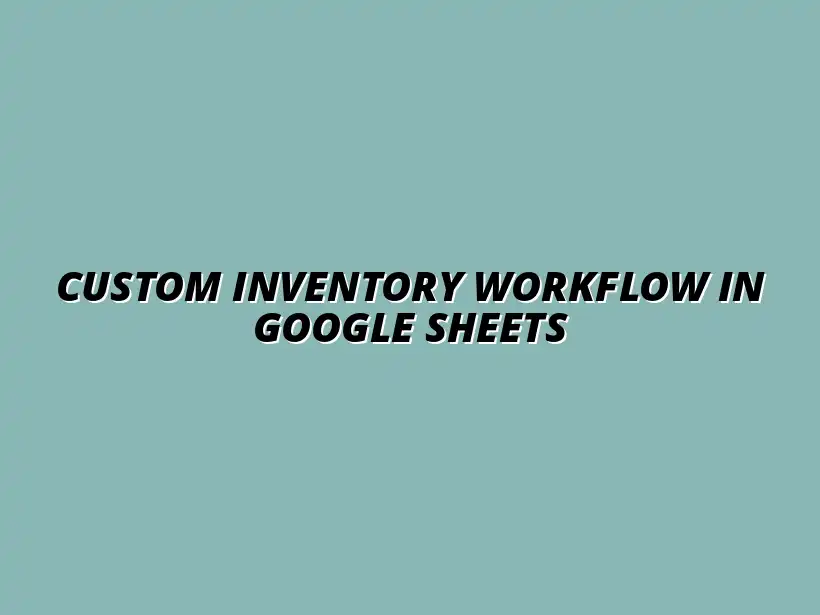
Custom Inventory Workflow in Google Sheets
Understanding Custom Inventory Management Needs
When it comes to managing inventory, every business has unique requirements that shape their processes. Understanding your specific inventory management needs is crucial for success. This involves recognizing what challenges you face and how tailored solutions can address those issues effectively.
In today’s fast-paced business environment, identifying the right tools and strategies to manage inventory can lead to significant gains. A custom approach allows businesses to not only track their stock levels accurately but also to align their inventory practices with overall business goals. Implementing a solution that fits your company’s needs can help streamline operations and improve overall efficiency. For example, learning how to manage inventory with Google Sheets can be a great starting point.
Identifying Core Inventory Management Challenges
Every inventory management system comes with its own set of challenges. Understanding these challenges is the first step toward finding effective solutions. Some of the most common issues that businesses face include:
- Inaccurate stock levels leading to overstock or stockouts
- Poor tracking of inventory movements
- Difficulties in forecasting demand
- Complicated manual processes causing delays
By pinpointing these core challenges, businesses can better evaluate their needs. This assessment allows for a more targeted approach when selecting or developing inventory management solutions.
Common Issues in Inventory Control
Inventory control is often fraught with problems that can disrupt operations. Some common issues include:
- Data Entry Errors: Manual entry can lead to mistakes.
- Inadequate Reporting: Not having the right data at your fingertips can hinder decision-making. Effective data visualization in Google Sheets can help improve reporting.
- Limited Visibility: Difficulty in tracking inventory across multiple locations.
- Supplier Delays: Issues with supply chain management can impact inventory levels.
Addressing these common issues is essential for maintaining a smooth inventory operation. Even small improvements can lead to significant time savings and enhanced accuracy!
Significance of Tailored Solutions
Finding a tailored solution for your inventory management challenges is not just beneficial; it’s essential. A one-size-fits-all approach often fails to meet the specific needs of a business. Customized solutions allow businesses to:
- Adapt to unique operational workflows
- Integrate with existing systems and software
- Provide real-time visibility and control over stock
- Enhance collaboration across departments
By investing in tailored inventory solutions, businesses can improve efficiency and reduce the risk of costly errors. This approach supports better decision-making and contributes to long-term success. For a deeper dive into effective inventory management strategies, check out this resource on managing inventory with Google Sheets.
Introduction to Google Sheets for Inventory Management
Google Sheets is a versatile tool that can transform how you manage your inventory. With its user-friendly interface and powerful features, it provides an accessible platform for creating custom inventory solutions. Understanding the benefits of using Google Sheets is the first step in streamlining your inventory management process.
By leveraging Google Sheets, you can easily collaborate with team members, track stock levels, and analyze data in real-time. This flexibility not only saves time but also promotes a more organized approach to inventory management!
Benefits of Using Google Sheets for Custom Workflows
Utilizing Google Sheets for inventory management brings a variety of advantages that can enhance your workflow. Here are some key benefits:
- Cost-Effectiveness: Google Sheets is free to use, eliminating expensive software costs.
- Accessibility: Access your inventory data from any device with internet connectivity.
- Customization: Tailor your spreadsheets to fit your specific business needs.
- Integration: Easily connect with other Google Workspace tools for a more seamless experience.
These advantages make Google Sheets a compelling option for businesses looking to enhance their inventory management processes. Who wouldn’t want a tool that’s both powerful and cost-effective? Learn how to streamline your workflow with Google Sheets for even greater efficiency.
Cost-Effectiveness and Accessibility
One of the standout features of Google Sheets is its cost-effectiveness. Businesses can utilize this tool without incurring any fees, making it an ideal choice for small to medium-sized enterprises. Additionally, the accessibility of Google Sheets allows for multiple users to access and update inventory data in real-time.
This means your team can collaborate effortlessly, ensuring everyone is on the same page. You’ll never have to worry about outdated information when your inventory data is available at your fingertips!
Collaboration Features of Google Sheets
Collaboration is vital in inventory management, and Google Sheets excels in this area. The platform allows multiple users to work simultaneously on the same spreadsheet. This feature is especially useful for teams spread across different locations or departments. For project management, consider using project management templates for Sheets.
Some collaboration features include:
- Real-time editing and commenting
- Version history tracking
- Shared access permissions
- Email notifications for updates
These features foster a collaborative environment, helping teams to manage inventory more effectively. With everyone contributing, you can expect better accuracy and improved communication!
Enhancing Your Custom Workflow with Automation
Automation can be a game-changer for your custom inventory management workflow. By leveraging tools like Google Apps Script, you can save time and reduce the chances of errors that often come with manual data handling. This section will explore how to integrate automation into your workflow and provide you with practical examples to enhance your inventory management.
With automation, repetitive tasks like data entry and report generation can be streamlined. This not only frees up your time but also allows you to focus on more strategic aspects of your business. Let's dive into how Google Apps Script can bring efficiency to your inventory processes! Learn to automate tasks with Google Sheets scripts for greater efficiency.
Integrating Google Apps Script for Advanced Automation
Google Apps Script is a powerful tool that allows you to write code for automating tasks within Google Sheets. This means you can customize your inventory management beyond basic functions. By setting up scripts, you can automate tasks that otherwise would require considerable manual effort.
Here are some common ways to use Google Apps Script to enhance your inventory management:
- Automating Inventory Updates: Automatically adjust stock levels based on sales or restocks.
- Generating Reports: Create periodic reports without having to manually compile data. Easily automate Google Sheets reports to save time.
- Notifying Team Members: Send automated emails or alerts when stock is low or when certain thresholds are met.
Automating Routine Tasks with Scripts
Automating routine tasks with scripts can make your inventory management much more efficient. Scripts can take over tedious jobs like checking stock levels or updating records. This way, you can ensure that your data is always current without having to constantly monitor it.
Consider these tasks that can easily be automated with Google Apps Script:
- Daily stock level checks.
- Weekly sales report generation.
- Monthly inventory audits notifications.
By automating these tasks, you can focus on growing your business instead of getting bogged down by routine data management.
Examples of Useful Scripts for Inventory Management
Here are a few examples of Google Apps Scripts that can be particularly useful for inventory management:
- Stock Alert Script: Sends an email alert when inventory falls below a certain level.
- Daily Summary Script: Compiles daily sales data into a summary sheet.
- Auto-Invoice Script: Generates and emails invoices based on sales recorded in your sheet.
These scripts can help streamline your inventory management process, making it easier to keep track of stock and sales.
Managing Your Inventory: Best Practices
Managing your inventory effectively is crucial for the success of your business. Implementing best practices can help you maintain accuracy and efficiency in your inventory management. In this section, we’ll discuss some of the most effective strategies to ensure your system remains robust and reliable.
Regular attention to your inventory system can prevent significant issues down the line. By following best practices, you can keep your inventory organized and responsive to your business needs!
Regular Maintenance of Your Inventory System
Just like any other system, your inventory management requires regular maintenance to function at its best. Scheduled audits and data cleanup can help ensure accuracy and identify inefficiencies. This practice is vital for maintaining a reliable inventory system.
Here are some regular maintenance tasks to consider:
- Conducting Scheduled Audits: Regularly check physical inventory against records.
- Performing Data Cleanup: Remove outdated or irrelevant information.
- Reviewing Supplier Performance: Assess and adjust supplier relationships as needed.
Scheduled Audits and Data Cleanup
Implementing scheduled audits helps in identifying discrepancies promptly. Additionally, maintaining clean data ensures that your inventory records accurately reflect your current stock levels. Regular audits, paired with thorough data cleanup, will keep your inventory system robust.
Consider setting a monthly or quarterly schedule for these maintenance tasks to keep your inventory management on track. This consistent check-in will pay off over time!
Staying Updated with Industry Trends
In the world of inventory management, staying updated with industry trends is crucial. Market shifts can affect inventory levels, supplier reliability, and customer demand. Keeping an eye on these trends will help you anticipate changes and adjust your strategy accordingly.
Here are some ways to stay informed:
- Subscribe to Industry Newsletters: Get the latest updates sent directly to your inbox.
- Join Professional Groups: Networking can provide insights from peers in your industry.
- Attend Webinars and Workshops: Learn about new tools and strategies from experts.
Staying informed enables you to make proactive decisions that can positively impact your inventory management.
Common Questions and Solutions
As you navigate your inventory management journey, you are bound to face challenges. Addressing common questions can help streamline your processes and clarify what to do in specific situations. Let’s tackle some frequently asked questions.
By understanding these common scenarios, you can ensure your inventory system operates smoothly and effectively.
How to Handle Inventory Discrepancies?
Inventory discrepancies can arise for various reasons, from data entry errors to theft. It’s essential to address these discrepancies promptly to maintain accurate records. Here’s what I recommend:
- Investigate the Discrepancy: Check for errors in data entry or miscounts.
- Adjust Records: Update your inventory system to reflect accurate counts.
- Implement Better Controls: Review and enhance your inventory tracking processes to prevent future issues.
What to Do When Inventory Levels are Low?
When you notice that inventory levels are running low, it’s essential to act quickly. Here are steps to address low inventory levels:
- Place Reorders: Contact suppliers for quick restocks.
- Review Sales Data: Identify fast-moving items to prioritize.
- Consider Safety Stock: Maintain a buffer stock to avoid stockouts.
Taking these steps ensures that you can meet customer demand without interruptions.
Final Thoughts on Custom Inventory Management Workflows
As we wrap up our discussion on custom inventory management workflows, it’s clear that continuous improvement is key. Your inventory management system should evolve with your business needs and market conditions. Embracing change will help you stay competitive!
Investing time in enhancing your workflow will pay off in improved efficiency and productivity in your operations.
The Importance of Continuous Improvement
Continuous improvement is essential for keeping your inventory management system effective. It involves regularly evaluating processes and seeking opportunities for enhancement. Feedback loops and adaptation strategies are crucial components of this process.
Consider incorporating these practices into your workflow:
- Solicit Feedback: Regularly ask your team for input on the inventory process.
- Monitor Performance Metrics: Track key indicators to identify areas needing improvement.
- Stay Flexible: Adjust your processes based on feedback and changing market trends.
Feedback Loops and Adaptation Strategies
Creating effective feedback loops helps you gather insights from your team and customers. Utilizing this feedback allows you to adapt your inventory management practices. Regularly review and update your strategies to keep pace with industry changes!
Remember, your inventory management workflow should be a living system that grows and improves over time. Be open to change, and encourage your team to share ideas for enhancement.
Encouraging Team Collaboration for Better Management
Encouraging teamwork can significantly enhance your inventory management process. A collaborative approach fosters better communication and shared responsibility. When everyone works together, it leads to more accurate inventory records and improved overall performance.
To promote collaboration, consider these steps:
- Hold Regular Team Meetings: Discuss inventory status and challenges openly.
- Use Shared Documents: Allow team members to update records in real time.
- Establish Clear Roles: Define responsibilities for inventory tasks to promote accountability.
Collaboration not only enhances your inventory management but also builds a stronger team spirit!